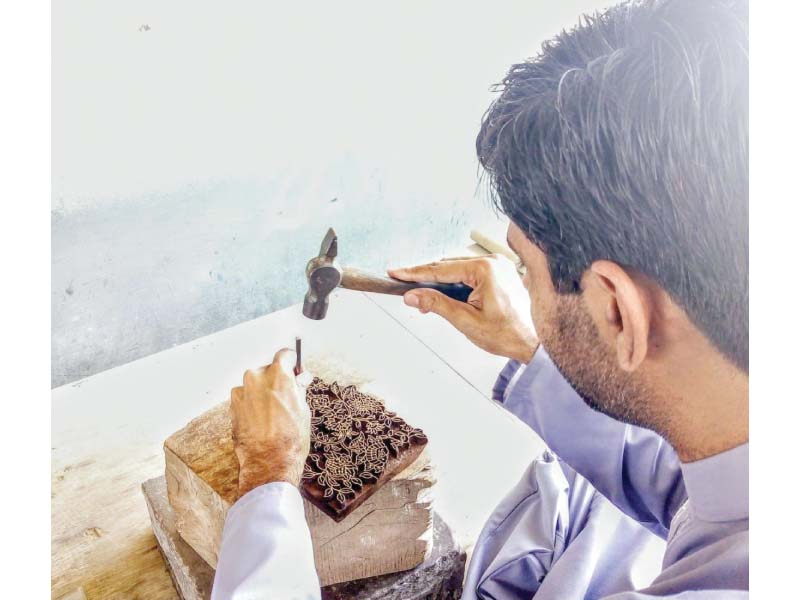
Ahmed, who runs a block printing shop in North Karachi, has been working since the age of 18.
The skill was passed on to him through generations, he told The Express Tribune, and now, when the block printing business has slumped across the country there is little else he can do to earn a livelihood. As a result, he sits at his shop all day long, seeing uninterested passers-by, hoping that maybe one of them would stop by to appreciate his craft and skill. Though, it seldom happens.
Finding it hard to survive the persistent slump in his business, he says that the situation is getting worse by each passing day, making it difficult for him to continue this work.
In the face of the dying craft of block printing, which Ahmed predicts would soon see its demise, he is one among the few remaining who have expertise in making blocks for printing.
The centuries-old skill of block printing finds its roots in China, from where it spread to the rest of the world including Pakistan. In fact, it has a long history in Pakistan as well, evident in the form of one of the prime examples of blocking printing, Ajrak, which dates many years back.
Apart from the typical geometric block print of Ajrak, another form of the craft which gained popularity in the Subcontinent, over the years, is that of block print embroidery. It involves tracing block print designs with hand embroidery.
Generally, block-printing mostly makes use of small blocks, made of Indian Rosewood or Sheesham. These blocks are referred to as Chaapay in the local vernacular and are etched with various design patterns which are inked and printed on fabrics.
According to Ahmed, these wooden blocks, or Chaapay, are prepared after a lot of hard work and the preparation spans over a period of many days. Explaining the arduous process, Ahmed said that the preparation of a single block takes around four to five days on average, which does not include the time required to etch patterns on the blocks and inking them with different colours.
He estimates that making a single block can cost anywhere between Rs500 and Rs30,000, depending on the design. Finer the design, more the cost, he says.
However, it is a pity that block printing has lost appeal among masses, laments Ahmed.
Block printing and hand embroidery, which dominated the textile design industry in Pakistan for many years, are now replaced by digital printing and embroidery. The demand for block printing is now limited to selected few circles comprising the rich and affluent. However, high demand among the affluent class does not warranty sufficient earning for block print artisans. This is because they don't directly deal with the end-consumers.
According to Yasir, who has expertise in creating embroidered block print designs, high-end brands and boutiques give orders for block printing to factories, in bulk. The end product, say a block printed kurta, is then sold for Rs2,500 to Rs3,000 but the artisan working in the factory is paid only a meagre Rs300 in comparison, he said.
Numerous boutiques have also set up their on workshops for block printing. They produce garments adorned with exclusive designs and patterns, which are preferred by the affluent and the elite, in a bid to don unique apparels. Similarly, designers have too started offering services for creating apparels embellished with customised block print designs, which are sold at high prices and exported as well.
Increased competition and decline in the overall demand for block printing has slowed down the business, for many like Ahmed and Yasir.
To add to it, block print artisans are further burdened by an increase in the price of raw materials.
A plank of Sheesham, which used to cost between Rs20,000 and Rs25,000 about a decade ago, is now priced between Rs100,000 and Rs150,000, says Ahmed, adding that the exponential surge in the cost of wood over time has increased the cost of Chaapay.
Consequently, block print artisans find themselves in a fix, unable to run their businesses with their rapidly shrinking incomes.
The artisans say that it becomes extremely difficult for them to make the ends meet and many of them have quit the profession, opting for alternative means of earning. Changing profession has brought in a stable income for them, yet they long for the craft they have left behind in order to survive the hard times, adding that had they received sufficient orders, earning Rs600 to Rs700 a day wouldn't have been too difficult but that was not to be.
Hence, they now sell bread on pushcarts, work as rickshaw drivers or have taken up jobs as salesmen. But they are not the only ones bearing the burden of a dying industry.
There are block print artworks created by students and graduates of art institutes, which are kept abandoned in dingy corners of rooms rarely visited.
And yet, there are veterans like Ahmed who prefer not to abandon the craft he inherited from his forefathers. Though, he has different plans for his children.
"My father and grandfather spend their lives earning a livelihood through block printing but the decline in business has convinced me not to let my children join the profession, which will end the years-long legacy of block printing in my family," he says.
Published in The Express Tribune, July 21st, 2019.
COMMENTS
Comments are moderated and generally will be posted if they are on-topic and not abusive.
For more information, please see our Comments FAQ