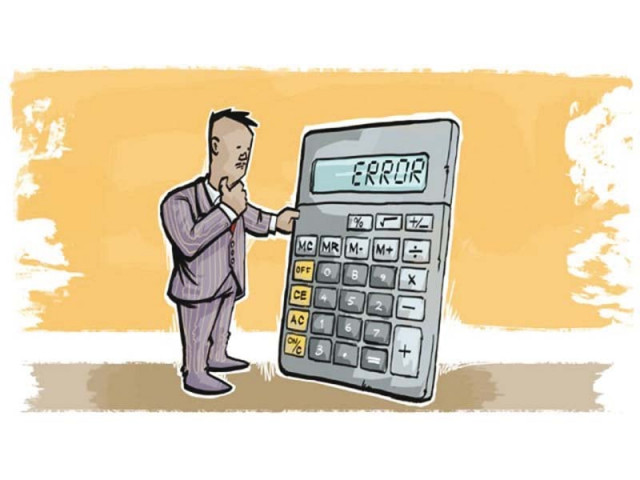
With such high proportion of value tied into their inventories, money can often be lost in inventories; to an extent, where only 3% higher cost of inventories can decrease profitability by more than 20%. I had urged the commodity type manufacturers to combat procurement frauds by using electronic weighing scales and connecting them with computerised vendor payment systems such as the one offered by modern ERP software.
Most ERP software has another clever trick up its sleeve. It reduces inventory costs and has dramatic effect on improving the profit margins. Like most things in manufacturing, it’s rather insipidly named as lot sizing. But it can save you millions.
Inventing the mathematics for lot sizing was groundbreaking work, performed by two geniuses - Dr Harvey Wagner, a mathematician from North Carolina University and Dr Thomas Within, a Princeton economist with tenures at Berkley and Wesleyan. Both toiled away to find the notoriously elusive solution. They succeeded in 1958 except that it wasn’t until the 1990s that computing power was cheaper and ubiquitous enough to allow for its widespread application in the manufacturing industry. The professors had performed their seminal work, happily one can assume, on a computer at Berkley which was the size of a basketball court.
I have been a smoker since my late teens. I crave cigarettes and being without them is a harrowing thought. So I hoard them. What the two professors did was to invent mathematics that I can use to answer the question - How many cigarettes I should buy and when? Should I rush to the nearest shop and buy a single stick, every time I want to smoke? Teenagers prefer a lot size of exactly one cigarette. Or should I buy a packet every day, a carton every week or 4 cartons every month? I have always preferred the latter as it addresses my insecurities well.
The lot sizing algorithm clearly thinks otherwise. After patiently feeding in the data into the software; minutiae such as the price of cigarettes, my daily intake, the driving distance of retail outlet from my residence, my income, duration of the trip to the shop, the fuel price, the current interest rate and even the cost of my cupboard, where I hoard them. The lot sizing algorithm recommended that I could save a few hundred rupees by buying 3 packs and 11 sticks every 4th day in January with other befuddling buying schedules for remaining months. I found these computer recommendations incredulous and dismissed them.
The manufacturing industry can’t afford to be dismissive. Their billions can be tied down in unused inventories that sit inside large warehouses, built on expensive land. They pay a huge cost of capital to acquire these inventories. Typically, much more than the interest rate. They also pay for its insurance; they spend money in building these storage facilities and pay their staff to watch over it. Their operations can grind to a halt, costing them millions in case a critical raw material runs out of stock. Ordering raw materials in just the right quantity is tightrope walking.
A well tweaked lot sizing software can provide the least cost solution to bedeviling questions. How many tankers of diesel should be ordered for the factory’s power plant and what should be their delivery schedule?
Or is it okay to buy 6,240 cotton bales now - an entire year’s supply for a typical spinning mill? Or will the spinner save more money by buying 17 bales every day? Or any number of permutations in between. This tussle has always been between temptations to hoard when the costs may escalate versus the cost of capital tied into inventories. The lot sizing is meant to solve exactly this problem.
The problem is further complicated by the consequences of hypothetical buying decisions taken previously. They tend to alter the remaining buying decisions. If you’re buying 240 bales tomorrow, then for the rest of your buying decisions, you can buy no more than 6,000.
For our spinning mills cotton buying decisions, there are exactly 132,860 permutations or ways in which the 6,240 bales can be ordered to cover for one year of operations. The beauty of lot sizing (if application of brute force by computers can be termed as such) is to systematically find every single hypothetical buying decision, project its impacts on future buying decisions and to determine the ordering cost as well as the holding cost of every decision. To cut it short, only 1 out of 132,860 possible decisions, has the least cost. Impressively, the Lot sizing software determines it within seconds.
It would seem that if you are a manufacturer and you take raw material buying decisions on daily basis, then it’s perhaps best to buy a lot sizing software, tweak it to perfection and then always do what the computer tells you to do. Your deference to both professors and your humility for your lot sizing software may save you millions in your inventory costs; albeit unhelpful if you’re a smoker.
The writer is an entrepreneur who has worked in Bangladesh’s garment sector
Published in The Express Tribune, July 27th, 2015.
Like Business on Facebook, follow @TribuneBiz on Twitter to stay informed and join in the conversation.
COMMENTS
Comments are moderated and generally will be posted if they are on-topic and not abusive.
For more information, please see our Comments FAQ