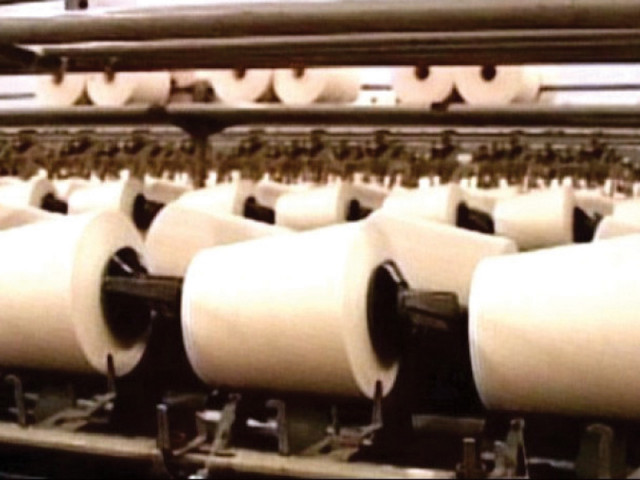
Spinning mills have actually been riding this wave for some months now, as more and more yarn is being demanded by China due to a spike in labour and raw material costs in the country. This has pushed Chinese yarn buyers to look to Pakistan and regional competitors for cheaper raw material.
“Crescent Cotton Mills already has three units up and running, while a fourth is in the process of being completed,” Crescent Cotton Mills Director Naveed Gulzar told The Express Tribune. Even as yarn exports continue to grow, it is difficult to say exactly how many companies will go for an expansion, he said, as that will be the decision of the individuals who run them.
Gulzar operates two mills in Punjab and another one in Sindh. His Sindh unit is performing better than the units located in Punjab, which Gulzar attributes to the relative abundance of gas supply in the southern province. “Our cost of production is lower by 60% in Sindh as compared to Punjab, because mills run on captive power plants which use gas as fuel,” he continued. “The cost is higher in Punjab due to the energy crisis and the cost involved in moving to alternative sources of energy,” he added.
A captive power plant typically generates electricity at the cost of Rs6.5 per unit, while the same unit costs a whopping Rs30 if generated using diesel as fuel, Gulzar said.
Omer Nazar Shah, CEO of Hassan Spinning Mills Faisalabad, agreed with Gulzar on his claim that units established in Sindh provide good returns because of relatively lower gas load-shedding in the province.
“Yarn has great demand in China, but 45% of our production has been affected due to the energy crisis,” he claimed. He added that even if companies run their mills at full capacity, they will be unable to fulfil the requirements of the Chinese market.
China has been relying on imported yarn for the last few years, Shah said. “This is an ideal situation for Pakistan, which has produces yarn in surplus to its needs,” he added.
Spinners told The Express Tribune that even small Chinese cloth printing mills are currently consuming around a million metres of gray (uncoloured) cloth per day. In comparison, Pakistani mills which manufacture gray cloth produce, on average, only 500-1,000 metres of fabric per day.
Published in The Express Tribune, May 29th, 2013.
Like Business on Facebook to stay informed and join in the conversation.
COMMENTS
Comments are moderated and generally will be posted if they are on-topic and not abusive.
For more information, please see our Comments FAQ