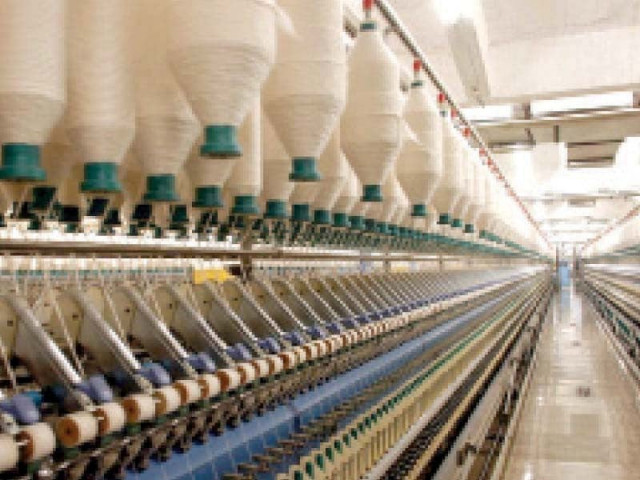
Pakistan’s economy pivots around two essentials, ie, textiles and energy because 60% of our exports constitute textiles, while 30% of imports comprise energy.
This becomes more critical when various studies project the export potential at $50 billion per year by 2030, though they were worth only $16.5 billion in FY 2022-23 with the historical maximum reaching $22.1 billion in FY22.
Some sources put this potential even at $100 billion. If realised, it can easily pull us out of the perennial malaise of the deficit in balance of payments, the primary cause of all of our economic woes. What further accentuates this inference is that the textile sector employs about 45% of the total labour force associated with the manufacturing sector.
Also, the industry is heavily dependent on cotton, therefore, any disturbance in the cotton crop also affects the performance of the sector and the economy.
Cotton’s challenges have only grown with time. Its yield was 615 kg per hectare in 1990 and 617 kg in 2020, which is a stark reflection of the poor performance in this segment, especially when China’s yield, now touching 2027 kg/hectare, grew by more than 150% during the said 30 years.
The decades of negligence in conjunction with the exponential rise in prices of natural gas and electricity over the past 18 months appears to have finally placed the industry on ventilator.
Expecting the bureaucrats managing such value chains to provide required solutions is a great fallacy. Devoid of the subject knowledge and required corporate leadership experience, they entirely lack the essential tools.
What further worsens this handicap is the fact that incompetence does not come alone; it also breeds intolerance, arrogance and cronyism and together they crowd all merit and professionalism out of the boardrooms. Isn’t this the story of our, almost, every PSE?
Factors affecting growth
Textile sector is plagued with several challenges, foremost being the rising production costs, particularly rooted in the double jeopardy of not only lack of reliable fuel supplies, but also higher prices. For instance, after the phenomenal rise of the industry during 2020-22, the increase in electricity prices in March 2023 immediately resulted in reversing the trend.
As a result, exports came down from $22.1 billion in FY22 to $16.5 billion in FY23 because the associated power tariffs were hiked from 9 cents/kWh to 17.5 cents/kWh. Gas prices have been raised by 223% since January 2023 till now. Another challenge is the lack of diversification. We still mostly rely on yarn and raw, unprocessed and unfinished ie, grey, fabric, which, due to marginal value addition, only fetches meagre profits.
While 63% of the global textile and apparel trade is now based on man-made fibres (MMF), however, as per pertaining annual report of the Textile Commissioner of Pakistan, synthetic fabrics contributed only 2.39% export earnings to the aggregate exports in FY21, while the contribution of cotton and cotton-based textiles remained at 97.1%.
One of the contributing factors appears to be the import duty structure for polyester staple fibre (PSF), the basic raw material required for MMF production. Thirdly; we lack in R&D. Unesco statistics tell us that Pakistan spends only 0.16% of its GDP on R&D, while India allocates 0.65% and Vietnam 0.43%. Also, an excellent study of PIDE tells us that 88% of the engineering firms in Pakistan do not allocate any funds, whatsoever, to this essential expense head.
The fourth factor is our general apathy towards environment. Toxic air emissions are a mammoth challenge. To remain eligible for supplying textile to the EU, Pakistan must begin transition towards net-zero emissions in earnest.
Another associated challenge is the discharge of chemicals-loaded wastewater from mills into water bodies because studies indicate that only 15% of Pakistan’s municipal and industrial wastewater goes through any treatment before disposal.
What is to be done
From the above analysis, it is obvious that if immediate remedial measures are not initiated, we may lose even the existing textile markets, let alone expecting any expansion.
An economy having the required depth and diversity in terms of value chains and value-added products may have been able to afford such a loss. However, in our case, when there is no other value chain which can even replace it partially, it would be nothing less than a socio-economic hara-kiri.
Therefore, it seems imperative to undertake the following steps on priority.
1) Identify and support techno-commercial options for the exploitation of indigenous sources of natural gas where conventional development is uneconomical. For example, possibilities exist where instead of transmission infrastructure, mini-LNG plants and LNG trucking may prove more feasible. Similarly, the development of some fields by deploying a hub strategy may prove more economical. 2) A few strategically located bio-methane plants in each textile district can help in mitigating natural gas consumption and associated costs.
3) Increase the consumption of grid electricity in the domestic sector, while targeting to possibly replace gas consumption, which may help in reducing capacity charges and diverting that gas to the textile sector.
4) Business units may consider undertaking energy audits ie, a rigorous ascertainment of their energy consumption on the basis of available industrial yardsticks and design efficiencies. They would be of further value if conducted in conjunction with management audits in the context of optimisation of workflow, performance logs, etc. This exercise may give surprises to owners with respect to cost optimisation opportunities. 5) Introduce automation and process design efficiencies in mills such as PLC systems, modern boilers, heat exchangers, etc.
6) More than 50% of our textile exports are made to the US and Europe. Therefore, managing the Carbon Border Adjustment Mechanism (CBAM) of the EU and the associated Carbon Border Tax, expected to be applicable by 2030, can throw a major challenge to our already fragile industry.
Thus, timely measures for monitoring and mitigating the emissions are imperative. Casual handling can lead us to meeting the same fate as that of PIA. The implementation can be financed by establishing a dedicated carbon credits market in Pakistan and green financing loans from the pertaining international institutions. 7) The industry may consider establishing centres of excellence, one each in Karachi, Lahore and Faisalabad, comprising a diploma institute for textile technicians and a training institute for grooming leaders for the industry.
8) Proactive adoption of synthetic fibres.
The writer is a Petroleum Engineer and an oil and gas management professional
COMMENTS
Comments are moderated and generally will be posted if they are on-topic and not abusive.
For more information, please see our Comments FAQ