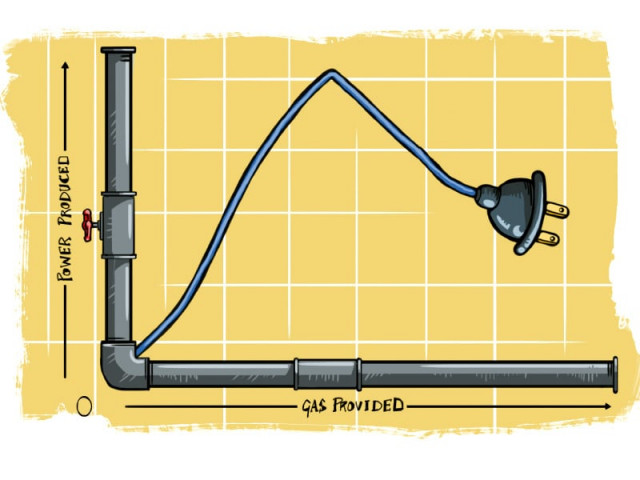
Caving in to the demands of the textile industry, the petroleum ministry has slashed the proposed energy efficiency requirements for captive power plants (CPPs) and natural gas boilers.
Earlier, in a guideline provided to gas utilities, the petroleum ministry had set a 50% efficiency benchmark for combined cycle plants and a 60% benchmark for gas engines and turbines based on cogeneration technology.
Sources said the textile industry had opposed the energy benchmarks set earlier, forcing the petroleum ministry to revise the benchmarks to make them more lenient. Industries deploying inefficient plants under the earlier guidelines may have had to face a higher gas tariff or had their gas supply disconnected.
In the latest summary sent to the Economic Coordination Committee (ECC) for approval, the petroleum ministry has now revised the proposed energy efficiency benchmarks downwards to 35% for combined cycle plants and 45% for cogeneration plants.
Gohar Ijaz, a prominent name in the textile industry, claimed that no power plants in the world could operate at 50% efficiency for combined cycle plants and 60% efficiency for cogeneration plants.
“Even new power plants, such as Saif, Orient and Halmore, have 50% efficiency,” he said; adding that a study conducted by the textile industry revealed that vehicles using CNG utilised gas with 10% efficiency rate; geysers at 6%; while fertiliser plants that use gas as feedstock consumed it at a 35% efficiency rate.
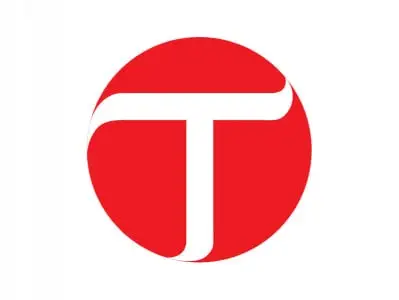
200 industrial units have currently deployed captive power plants that generate a total of 3,000 megawatts of power. “We have agreed that gas utilities can charge a higher differential tariff from captive power plants with low efficiency rates,” he added.
During audits, captive power producers which fail to achieve even the revised efficiency benchmarks will additionally be given three months to improve their performance. In case they are not able to do so, they will be given a grace period of another three months; with an option to pay a penalty equivalent to the tariff notified by the Oil and Gas Regulatory Authority, or face disconnection.
In the audit exercise, the auditors will compare natural gas consumption and bills in relation to the number of energy equipment, explained sources.
Sources said that the petroleum ministry had informed the ECC that the textile industry requires a long-term energy plan, and that they should be informed beforehand which technology needs to be installed in the future. More importantly, such information must be shared with the Ministry of Textile on an urgent basis.
The spinning industry should also be encouraged for downstream investment so that they can utilise heat from their plants efficiently, the ministry said. Alternatively, other options may be explored for the spinning industry, such as the installation of low pressure plants that utilise heat dissipated from the main plant.
The petroleum ministry has also proposed a relaxation in import duties on energy-related equipment so as to attract further investment. It has also said that the current standards may be revised after two years to urge an improvement in the efficiency of such plants.
Published in The Express Tribune, December 11th, 2012.
COMMENTS
Comments are moderated and generally will be posted if they are on-topic and not abusive.
For more information, please see our Comments FAQ