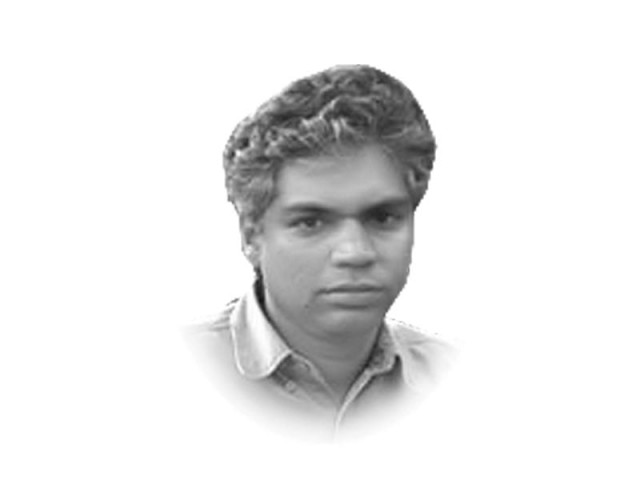
In the case of the engineering colleges, the situation is not surprising. A national employability survey this year reported that only about one in six engineering graduates is employable. There are, possibly, half a million engineering graduates emerging from these colleges every year, but the National Association of Software and Services Companies (Nasscom) gripes on and on about impending shortage of employable engineers. Only one of India’s top-rated engineering colleges figures in Asia’s top 200.
Our politicians, encouraged by a few economists, often talk of the GDP in terms of the great “demographic dividend” to come by 2020, when more than 250 million Indians between the ages of 15 and 25 years will work and earn. But that might as well turn out to be the real problem. Where are the jobs? Not all of them will be engineers, employable or otherwise. The bulk of them will be farm-to-work or school-to-work poor, without skills to find employment in the cities and towns. In Bangalore, the software centre of India, many such people drive cabs and clean floors, but even these jobs will get scarce with the continued migration from villages to cities.
A working group set up by the government last year to recommend schemes to boost India’s exports stated plainly in its report: “Many advanced and developing countries followed a path of classical transformation of their economies from primary (agriculture and allied) to secondary (manufacturing) and tertiary (services) in successive stages. The share of the manufacturing sector in the GDP increased over time and in the process, the sector absorbed people migrating from agriculture for better employment prospects. However, in the case of India, the development process appears to have skipped the second stage of economic transition (industrial sector growth), moving directly to growth in the services sector.”
Clearly, India’s years of obsession with the ‘soft’ sectors like software and IT services, handling of clerical and business processes for clients abroad, have hurt its essentials. The economic growth of 20 years has been accompanied with the gradual decline of the old industrial sectors. As the government watches China with envy, India’s industry and manufacturing sector continues to return gloomy data. “The industrial output reading is just the latest data point suggesting a loss of momentum in Asia’s third-largest economy,” the Wall Street Journal noted this week. The ‘soft’ services sector has created great wealth for some individuals and employment opportunities for about one and half million engineers, but eventually hurt the Indian manufacturing sector and the overall economy. Because it needs English-speaking employees who are familiar with computers, it hires engineering graduates for other-than-engineering skills, in call centres and process jobs. The skills are critically required elsewhere, to build roads, drains and dams; to run factories and make goods. They hire them on salaries that the manufacturing sector cannot match because the clients abroad pay in dollars.
But now, there is a new national manufacturing policy. The policy actually marks a shift from India-shining fantasies to the blue-collar vision, where millions make the economy and take from it. They will grow exports and be the market, too. The policy firmly states that only good old manufacturing will offer large employment options to the 200 million who will need the jobs in the next 10 years. It offers tax benefits and incentives to manufacturing and engineering companies to start their own training centres to develop the skills they need to employ. The preference will be for local people and the courses and hands-on training will be in the local languages. In the next 10 years, the policy aims to create employment for 100 million people. It is back to basics — the factory floor.
Published in The Express Tribune, September 14th, 2012.
COMMENTS
Comments are moderated and generally will be posted if they are on-topic and not abusive.
For more information, please see our Comments FAQ