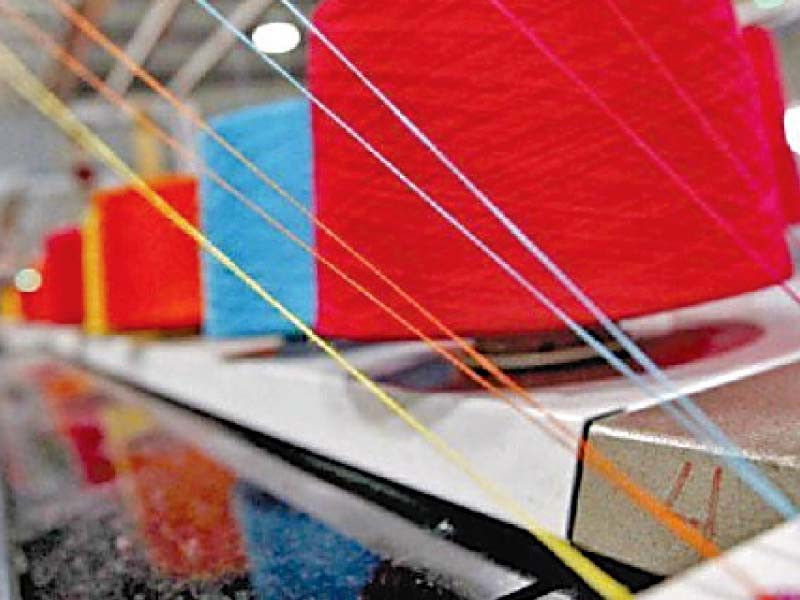
Pakistan’s Textile Value Chain (TVC), a cornerstone of the economy, is undergoing a transformative journey. As the nation’s largest and oldest manufacturing industry, it plays a crucial role in sustained exports and GDP contribution, aligning with global trends for accountability and business optimisation. Despite textiles being a major player in Pakistan’s economy, a significant number of firms still operate in a non-integrated structure. Nevertheless, the industry successfully exports a substantial percentage of its total output. In integrated sectors, each participant contributes to the value addition of textile goods.
The paradox of a long-standing economic powerhouse with predominantly non-integrated factories highlights both the resilience and challenges encountered by the Textile Value Chain (TVC) in Pakistan. Pakistan is a major producer, consumer, and exporter of cotton yarn globally. However, the average size of spinning mills in Pakistan is comparatively smaller than the global standard, making them less competitive, particularly with small spinning units using outdated technology and producing yarn counts below global market demands.
Integrated textile factories offer several advantages contributing to operational efficiency and product quality. However, they face challenges such as being capital-intensive, less responsive to technological advancements, and susceptible to disruptions that can impact the entire production process. In the context of a multistage turnover tax, non-integrated factories face increased gross taxes compared to their integrated counterparts. This discrepancy arises from the unique tax structure in non-integrated industries, imposing a turnover tax at each production stage. Consequently, as a product advances through multiple factories, cumulative taxation occurs, leading to an increased cost for the final product, making the non-integrated sector less competitive and diminishing profits.
Read Pakistani textile innovation shines at Heimtextil 2024
Moreover, sales tax collection mechanisms vary between integrated and non-integrated factories. Integrated factories often benefit from a sales tax advantage due to comprehensive reporting throughout the entire production process, while non-integrated units suffer from reduced transparency, resulting in a diminished refund of sales tax at the final export stage. According to IMF reports, the inclusion of certain cost elements into the product price, facilitated by the sales tax capture refund on exported goods from non-integrated factories, renders the final product less competitive. This complexity in the tax landscape influences the competitiveness and operational efficiency of both integrated and non-integrated industrial entities.
The imposition of duties on raw materials exacerbates challenges for Small and Medium-sized Enterprises (SMEs), particularly as they struggle to avail duty-free benefits in the export duty structure. Large, well-integrated firms can take advantage of duty exemption schemes for exporters, while smaller enterprises face difficulties utilising these tools due to the complexity of application processes. Consequently, SMEs find it challenging to compete, as these duties significantly inflate production costs throughout the manufacturing process, creating a barrier to competitiveness. This hampers their innovation to align with global trends, limiting their ability to offer cost-effective products and contributing to the existing textile trade imbalance in Pakistan.
Financial institutions naturally consider SMEs riskier due to their smaller size, limited track record, and insufficient collateral. Consequently, SMEs face difficulties obtaining loans or credits on favourable terms. Integrated factories, on the other hand, enjoy potentially easier access to credit due to their more comprehensive and stable business model.
Flexibility is a key aspect worth noting, particularly in integrated textile industries, where importing for re-export can enhance efficiency and ensure a steady supply of raw materials. It’s an important consideration, albeit one that may heighten dependence on foreign suppliers. In contrast, non-integrated industries might prioritise domestic sourcing for better control. However, when these non-integrated industries engage in importing for re-export, they could encounter coordination challenges.
Read The dream of 200% growth in textile exports
Lastly, traceability in the Pakistani textile industry varies. Integrated factories benefit from easier traceability due to the centralised nature of their production process, while non-integrated factories may find traceability more challenging due to the involvement of multiple entities in different stages of production. On the other hand, non-integrated textile factories offer several advantages, most notably specialisation. By focusing on specific stages of the production process, these factories can achieve a high level of expertise and efficiency in their chosen areas. This focused approach allows for targeted resource allocation, contributing to a more sustainable and energy-efficient manufacturing model. The model also allows for increased flexibility, enabling quick adaptation to market demands and technological advancements. Additionally, the distribution of risks across different stages mitigates the impact of failures, enhancing the overall resilience of non-integrated factories.
The discourse on integrated versus non-integrated textile units is also important in terms of sustainable practices. The impact of processes like picking, transportation, and ginning on cotton quality is particularly relevant here. Integrated units have the potential to implement more coordinated and sustainable practices across these stages. This comprehensive approach allows for better control over the entire supply chain, leading to improved cotton quality and reduced environmental impact. In contrast, non-integrated units face challenges in maintaining consistent and sustainable practices throughout the entire cotton processing cycle. Addressing sustainability concerns in these processes becomes imperative for both integrated and non-integrated units in Pakistan, emphasising the industry’s need to adopt eco-friendly methods and ethical sourcing practices to ensure the production of high-quality and environmentally responsible textiles.
Read SHC temporarily suspends gas tariff hike for textile industry
Non-integrated textile factories face severe challenges like a lack of communication between different entities involved in the production process. Pakistan’s standalone spinning units are increasingly becoming incompatible with competitors. Globally, textile industry enterprises are moving towards full or partial integration. To remain competitive and relevant in the evolving textile sector, Pakistan should align itself with this trend. This is imperative for standalone spinning units to integrate and diversify their offerings. Integration is not just a necessity but a crucial imperative for survival in the competitive landscape. Pakistan’s textile sector, with its numerous units and challenges in small spinning units, leans towards non-integration. They should address issues of outdated technology and credit access. In contrast, Bangladesh’s textile industry, represented by the Bangladesh Textile Mills Association overseeing yarn manufacturing mills and fabric manufacturing mills, demonstrates a higher level of integration, fostering collaboration across different stages. Meanwhile, India’s textile landscape, marked by an extensive number of mills and extensive capacity, indicates a substantial degree of integration.
In conclusion, integrating Pakistan’s textile industry, particularly SMEs, with track and trace systems is crucial for leveraging the GSP+ status and expanding into new markets. The establishment of the National Compliance Centre marks a significant step towards improved traceability and compliance standards, essential for enhancing the sector’s competitiveness and sustainable growth. However, more comprehensive measures and strategic policies are required to bridge this gap and foster sustained growth in the export sector.
SHAHID SATTAR HAS SERVED AS MEMBER ENERGY OF THE PLANNING COMMISSION AND HAS ALSO BEEN AN ADVISER AT THE MINISTRY OF FINANCE. AMNA UROOJ WORKS AS A RESEARCH ANALYST AND HAS AN MPHIL IN PUBLIC POLICY FROM PIDE
Published in The Express Tribune, January 15th, 2024.
Like Business on Facebook, follow @TribuneBiz on Twitter to stay informed and join in the conversation.
COMMENTS
Comments are moderated and generally will be posted if they are on-topic and not abusive.
For more information, please see our Comments FAQ