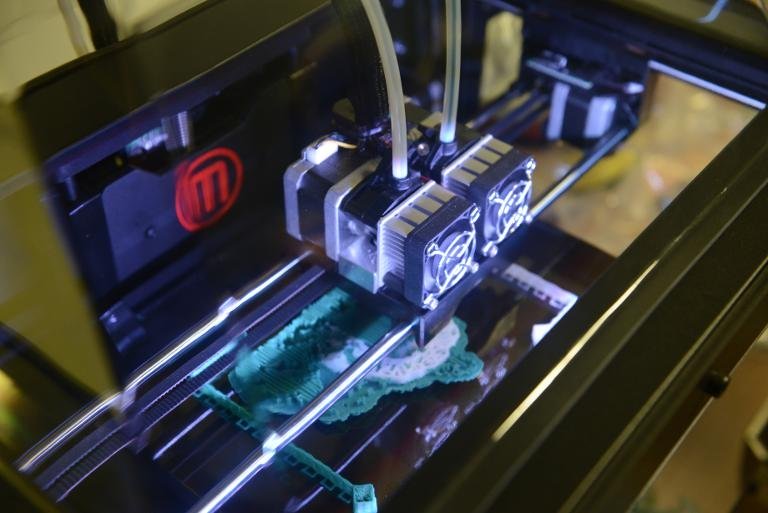
For many, 3D printing still looks like a gimmick, used for printing useless plastic figurines and not much else.
But with key patents running out this year, new printers that use metal, wood and fabric are set to become much more widely available, putting the engineering world on the cusp of major historical change.
The billion-dollar defence industry is at the bleeding edge of this innovation, with the US military already investing heavily in efforts to print uniforms, synthetic skin to treat battlewounds, and even food, said Alex Chausovsky, an analyst at IHS Technology.
Scientists at the Massachusetts Institute of Technology have already invented "4D printing", creating materials that change when they come into contact with elements such as water.
One day, that could mean things like printed uniforms that change colour depending on their environment.
In the real world, the baby steps are already being taken.
Late last year, British defence firm BAE Systems put the first printed metal part in a Tornado jet fighter.
The company recently put out an animated video showing where they think such humble beginnings could one day lead.
It imagined a plane printing another plane inside itself and then launching it from its undercarriage.
"It's long term, but it's certainly our end goal to manufacture an aerial vehicle in its entirety using 3D printing technology," Matt Stevens, who heads BAE's 3D printing division, told AFP.
But the real revolution of 3D printing is less about the things you can make and more about where you make them.
Being able to take printers to a warzone promises a radical shake-up of combat and the defence industry, says Peter W Singer, an expert in future warfare at the New America Foundation.
"Defence contractors want to sell you an item but also want to own the supply chain for 50 years," he says.
"But now you'll have soldiers in an austere outpost in somewhere like Afghanistan who can pull down the software for a spare part, tweak the design and print it out."
This could lead militaries to cut out private defence companies altogether. And by combining 3D printing with assembly line robotics, those that remain will be enormously streamlined.
That sort of disruption carries huge political implications in places like the United States (US) where defence firms are purposefully spread around the country and support millions of jobs.
"The Pentagon and defence industry have an incredibly tough time with innovation, but you don't want to wait to lose a major battle before you do it," says Singer.
3D printing could even change foreign policy, for instance by undermining sanctions.
"The US has sanctioned everything from fighter jet spare parts to oil equipment. 3D printing could turn sanctions, which have been a crucial part of foreign policy for a generation or more, into an antiquated notion," says Singer.
Then there are the scarier prospects that come with reducing the barriers to arms manufacturing.
"Think of master bombmakers making new designs that look like everyday products or a lone wolf operator printing a plastic gun he can get past security at the White House," says Chausovsky.
But all of that may pale in comparison to the security risks that 3D printing could trigger by revolutionising economies.
If anyone can print retail goods, economies that rely on cheap factory labour to make things like clothes and toys may find themselves in deep trouble, with all the security consequences that go with that.
"If you want to know where the big threat of 3D printing is, think about how reliant China is on its low-cost merchandising sector," says Chausovsky.
3D printing, invented in the 1980s, is much older than many realise.
The recent upsurge in interest is tied to the fact that patents on the original technology are expiring, opening the way for competition that will drive up quality and push down prices.
The first major patents to run out were in 2009 for a system that used plastics known as "fused deposition modelling".
But the next big ones, that expired in the first half of 2014, are related to "selective laser syntering" that prints metals such as aluminium, copper and steel, and with much greater definition.
And rather than working with solid lumps of metal, engineers can create complex new shapes that use much less material without losing any strength.
"You can't drill a curved hole," says Chausovsky. "With 3D printing, you're creating products that would never be possible with traditional methods.
The full implications are still hard to imagine.
"It's the first time in a very long time that there's been such a radical shake up in industrial engineering," says Stevens at BAE. "We're not just improving things, we're re-writing the rule book."
COMMENTS
Comments are moderated and generally will be posted if they are on-topic and not abusive.
For more information, please see our Comments FAQ