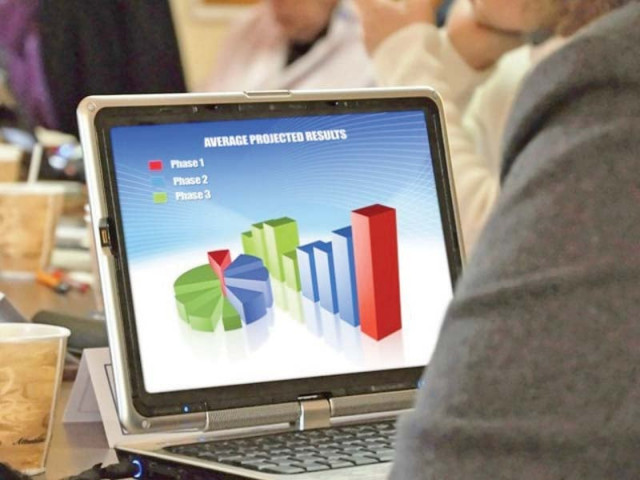
Manufacturing can be considered as a flow of raw materials and components through processes that consume them to produce intermediate products. The latter become components for subsequent processes, where yet more raw materials flow in, producing more intermediate products.
Whatever the end product or its complexity, the most important challenge is to procure components in the right quantity and to make them available at the right time. Any missing material will halt production and starve the next process.
Thus, creating a domino effect where progressively all downstream processes would be forced into a shutdown. The labour and the machines would sit idle, losing millions in a matter of days if not hours.
To shield operations from such calamities, procurement managers typically overcompensate by ordering more raw materials than they actually need. This action triggers another serious problem of high inventories – cash invested into material purchases, sitting idle in the warehouse.
Manufacturers around the world operate on high volumes, high capacity utilisation and thin margins of less than 10%; rarely can they act like the stunningly profitable Apple Incorporation, selling its iPhones at 70% margins. For most, material purchases may cost 50% to 70% of the revenues.
Idle money sitting at warehouses is known as the carrying cost, this is the cost of capital and warehousing put together. The cost accountants conservatively estimate it at 18% to 30% of purchase value. This can potentially knock off a third of profits.
Always in a catch-22, a failure to purchase raw materials causes unplanned shutdowns while buying them in excess increases inventory carrying costs. It seems that efficient manufacturing boils down to solving essentially a mathematical problem ie correctly calculating what materials are needed, combined with their quantity and the time of usage.
Surely, this could not have gone unresolved by the 250th anniversary of industrial revolution. Except that, until the beginning of the computer revolution in the 1960s, there were no computing devices that could solve this problem fast enough for a manufacturer.
Birth of MRP
Indeed, the computer programmable logic of Material Requirement Planning (MRP) was invented in 1970. Its algorithm takes massive amounts of data for each and every level of manufacturing.
For complex products, MRP answers the processes required for each material. The answers are generated automatically in the form of purchase requisitions and hundreds of job orders telling each department which job to work on and when. Clearly, humans cannot do such massive data crunching but computers certainly can.
Using modern servers with new generation processors, the MRP can perform millions of calculations in less than a second and can provide multiple material requirements in real time instead of struggling every weekend.
In fact, the use of MRP is so ubiquitous in the developed countries that it is hard to imagine any manufacturer not using it. It is commercially sold as ERP – the enterprise resource planning – software.
In Pakistan, various brands, together with their local partners, have been implementing them for at least two decades now. A typical ERP implementation for a mid-sized manufacturer may cost more than $200,000. By now all the multinationals and most of the local blue-chip manufacturers use ERPs. This still represent less than 200 manufacturers out of more than 20,000 in the country.
Ducking the challenge
However, there is a lazy way to dodge this manufacturing challenge by manufacturing only simple products, preferably the one that involves no more than a few simple processes and the least number of raw materials and components.
We manufacture tractors, buses, cars and motorcycles by importing nicely packed completely knocked down kits. The challenge of planning for materials is conceded to the foreign principals. Others opt for commodity involving least number of processes and materials.
In this overpopulated bandwagon, only the producer with the least cost survives. These products yield meagre profits which quickly turn into losses when another least-cost producer emerges.
In this day and age, all complex products can be ultimately broken down into relatively simple components, something any machinist or a repairman would testify to. Individual components can be copied and sourced to smaller sub-contracted manufacturers.
Gujranwala is just such a town with its genius of copying components, flawlessly. Much to the west’s grief, Chinese have made entire careers out of copying and reverse engineering.
However, what remains a pervasive challenge is organising manufacturing supply chains involving hundreds or even thousands of components. The only way out of this huge challenge is to put to use modern computing technologies like packaged ERP software.
Here, most of our local manufacturers fail spectacularly to leverage them. They dumb down their products and keep them simple and manageable.
The writer is an entrepreneur who has worked in Bangladesh’s garment sector
Published in The Express Tribune, March 30th, 2015.
Like Business on Facebook, follow @TribuneBiz on Twitter to stay informed and join in the conversation.
COMMENTS
Comments are moderated and generally will be posted if they are on-topic and not abusive.
For more information, please see our Comments FAQ